Geprinte Vergaderfabriek met Biofoam isolatie
Op 30 januari 2019 kon eindelijk de 3D-betonprinter starten met het printen van de Vergaderfabriek in Teuge. In tien dagen zijn alle wanden geprint, waarna de verdere afbouw is begonnen. Zo worden er nog grillig gevormde 3D geprinte betonnen schaaldelen tegen de gevelelementen en op het dak geplaatst, waardoor de uiteindelijke blobvorm ontstaat. Koston Nederland BV vulde de bijzondere gevelelementen met HR++BiofoamPearls®.
Tekst: ing. Frank de Groot
Beeld: Mediavisie

3D-betonprinter print een wand voor de Vergaderfabriek.
De wanden van de Vergaderfabriek worden geprint door Cybe. Dit innovatieve bedrijf is in 2013 opgericht door de nog jonge Berry Hendriks. Hij was tot die tijd, net als zijn twee broers, nog werkzaam in het bedrijf van zijn vader: Hendriks Bouw in Oss. In het najaar van 2017 sprak BouwTotaal hem over zijn visie op 3D betonprinten: “Het viel me in het bedrijf van mijn vader al snel op dat het enorm veel tijd kost om een bouwproject te realiseren. Het kost bijna een half jaar om te komen tot het definitief ontwerp en de aanvraag omgevingsvergunning. Die tijd is sterk te verkorten door alle disciplines, zoals architect, constructeur, W- en E-installateur, tegelijkertijd rond de tafel te zetten en het ontwerp in BIM uit te werken. Maar dan wordt vervolgens op de bouwplaats alles met de hand gemaakt.”
“De voordelen van betonprinten op de bouwplaats zijn groot. Je hebt minder mensen nodig, waardoor je een antwoord biedt aan het nu al grote tekort aan vakmensen. Daarnaast is er veel minder transport nodig van bouwmaterialen en het totale bouwproces wordt veel korter”, aldus Berry Hendriks. Overtuigt van de mogelijkheden richtte de jonge innovator in 2013 CyBe op, om vanuit dit bedrijf het 3D printen verder te ontwikkelen.

Artist impression hoe de Vergaderfabriek eruit komt te zien. Beeld: THE FORM FOUNDATION.

Artist impression hoe de Vergaderfabriek eruit komt te zien. Beeld: THE FORM FOUNDATION.
Ervaring in binnen- en buitenland
Inmiddels is er in 2017 in de woestijn van Dubai een compleet geprint betonnen gebouw opgeleverd: the R&Drone Laboratory. Dit 14 x 12 meter grote R&D laboratorium staat in bij een nieuw solarpark en is in opdracht van Dubai Electricity and Water Authority (DEWA) gebouwd. In Saudi-Arabië werd in 2018 een éénkamerwoning van 80 m2. Het is de eerste van naar verwachting nog veel meer 3D geprinte woningen, omdat de overheid van dit land de ambitie heeft om tot 2030 circa 1,5 miljoen woningen met innovatieve technieken, zoals 3D betonprinten en metselrobots, te realiseren.
In Milaan verrees vorig jaar verder een vier kamerwoning. Ook werd een betonprinter geleverd aan een grote prefab betonproducent in Japan met ruim 28 productielocaties. Hiermee worden in eerste instantie toiletten, inspectieputten en andere prefab elementen voor bruggen en gebouwen.
In Nederland produceerde Cybe voornamelijk inspectieputten voor M.J. Oomen (KWS), een voetbrug, banken en testwanden.
Tijdens het gesprek met BouwTotaal in het najaar van 2017 was het nog de verwachting dat het printen van de vergaderfabriek in het eerste kwartaal 2018 zou kunnen starten. Maar halsstarrige bouwregels en technische problemen zorgden voor flinke vertraging. Zo ontbreken er normen en richtlijnen voor het gebouw in Teuge. Daardoor moesten proef elementen worden gemaakt, waarop testen zijn uitgevoerd. Een uiteindelijke belastingproef bij TNO begin januari 2019 toonde aan dat het proefpaneel twee keer zo sterk was als gedacht. De gemeente bleek daardoor bereid de proefresultaten als gelijkwaardige oplossing te beschouwen, waardoor een omgevingsvergunning werd verstrekt.
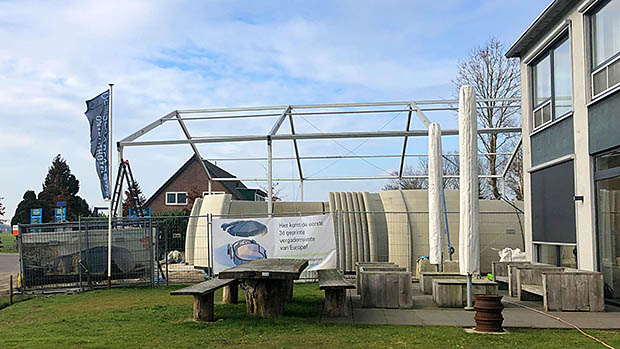
De elementen zijn in een tent geprint, zodat de robot was beschermd tegen weersinvloeden.
Zeer hoge treksterkte
Niet alleen de 3D betonprinter is van belang, maar ook de toegepaste mortel. De mortel die CyBe gebruikt heeft een circa zeven keer hogere trek- en buigsterkte dan traditioneel beton. Bovendien wordt na 24 uur al uitgehydrateerd, terwijl dit bij traditioneel beton pas na 28 dagen (!) is. “Een hoge aanvangssterkte is nodig, omdat de geprinte lagen anders te veel uitzakken. Een muurelement van 3 bij 4 meter wordt binnen 2,5 uur geprint.”
De hoge trek- en buigsterkte worden onder meer wordt bereikt door de juiste cementkeuze en toeslagstoffen. De maximale korrelgrootte van het grind is 3 tot 5 mm, omdat het anders niet verpompbaar is. Verder worden er geen staal- of kunststof vezels toegevoegd om de sterkte te verhogen.
Waarom dan niet overal dit wonderbeton toepassen? Hendriks: “Deze betonmortel is niet aantrekkelijk voor de traditionele bouw, omdat deze duurder is door de eigenschappen als de grote treksterkte. Wij printen holle wanden met hoge sterkte, waardoor er zes tot zeven keer minder beton nodig is. En je hebt ook alleen een operator op de bouwplaats nodig. Je hebt geen kosten voor het stellen van bekisting, betonstorten en transport. Het hele proces verandert mee.”

De holle ruimten in de gevelelementen zijn na het printen door Koston Nederland BV succesvol gevuld met HR++BiofoamPearls® van Termokomfort.
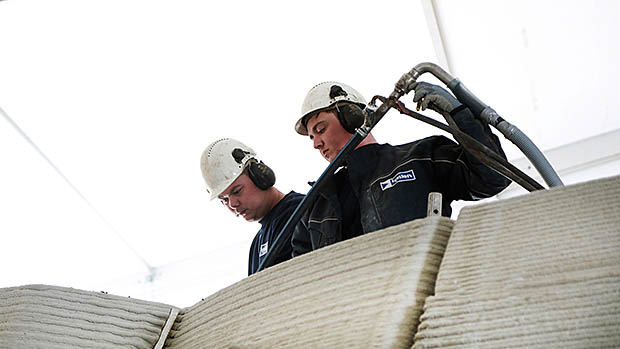
De holle ruimten in de gevelelementen zijn na het printen door Koston Nederland BV succesvol gevuld met HR++BiofoamPearls® van Termokomfort.
De Vergaderfabriek
Op woensdag 30 januari 2019 plaatsten leerlingen van De Zaaier in Teuge bij wijze van starthandeling een tijdscapsule in de holte van de eerste 3D-betongeprinte muur van De Vergaderfabriek. De tijdcapsule bevat brieven gericht aan de toekomst en treedt in werking als het gebouw in de toekomst gerecycled gaat worden. Het ontwerp is van Pim van Wylick van The Form Foundation. Opdrachtgever zijn Marjo en Arvid Prigge van De Slaapfabriek uit Teuge (MKB) en Centre4moods (startup). Zij hebben onder het motto ‘Ontwaak in een nieuwe wereld’ een totaal nieuwe visie op trainen en vergaderen ontwikkeld. Door te kiezen voor 3D-betonprinten kan volledig vrij gebouwd worden in ronde en gebogen vorm die direct aansluit op de wensen van de gebruikers. Op de gekromde wanden vinden straks projecties plaats die de sfeer oproepen die past bij de aard van de bijeenkomst. Dat wordt versterkt door geuren die worden verspreid. Zo kunnen straks zee-, bos, stads- en een hele reeks andere landschappen worden opgeroepen.
Het gebouw is 100 m2 en gaat dienst doen als vergader- en presentatieruimte voor 25 mensen. Printen van het gebouw moet, in vergelijking met de traditionele bouw, leiden tot 40 procent minder CO₂, 70 procent minder afval en een veel korter bouwproces voor gebouwen met een complexe vorm. De wanden va het gebouw zijn in tien dagen geprint. Dat gebeurde in een tent, om de robot te beschermen tegen weersinvloeden. De wanden van het ‘blobvormige’ gebouw zijn hol en zijn na het printen met isolatie gevuld. De negen wandelementen zijn ongeveer 3 meter hoog en 4 meter breed. De karakteristieke printlaagjes worden aan de binnenkant vlak afgewerkt door stukadoors. Na het printwerk rolde de printer op zijn rupsbanden naar buiten door een raamopening.
Isolatie gevelelementen
De holle ruimten in de gevelelementen zijn na het printen door Koston Nederland BV succesvol gevuld met HR++BiofoamPearls® van Termokomfort. Dit is een op EPS lijkende isolatieparel, vervaardigd uit melkzuur. Deze is biobased, C2C gecertificeerd en heeft een hele lage CO2-footprint. Termokomfort neemt al haar producten na afbraak van een constructie terug en hergebruikt dit in nieuwe producten of recyclet dit in de coöperatieve recyclingfabriek in Terneuzen. Bij de Biofoam® producten is het eventueel ook nog mogelijk om dit industrieel te composteren waardoor de cyclus volkomen rond is. BioFoamPearls zijn breed toepasbaar als dak-, spouw- en vloerisolatie in zowel bestaande bouw als nieuwbouwwerken.
Niet alleen door de lage CO2-footprint viel bij dit project de keuze op deze isolatieparels. De parels klinken namelijk ook niet in en kunnen tevens ingeblazen worden. Voordeel is verder de volledige vormvrijheid. Samen met de hele lage CO2-footprint, en het speciaal vervaardigde beton dat voor het printen is gebruikt, past dit materiaal precies in de bouwvisie van het project.
De isolatie is door Koston Nederland B.V. met behulp van een inblaaspistool aangebracht via de bovenzijde van de wandelementen. Deze zijn na het printen van de elementen nog gewoon open en de BioFoamPearls konden daardoor zonder te hoeven boren worden aangebracht. Het aanbrengen van 40 m3 isolatiemateriaal kostte hier slechts één werkdag met twee personen. Ook heeft men tijdens het vervaardigen van de geveldelen geen rekening hoeven te houden met de isolatie en had men dus volledige werkvrijheid met de bewapeningen /verankering. Dit vereenvoudigt en versnelt het bouwproces enorm.
Omdat de wanddelen ronde ‘natuurlijke’ vormen hebben is de wanddikte niet overal gelijk: deze varieert tussen de 25 en 70 cm. De Rc-waarde ligt hierdoor tussen 6,5 en maar liefst 18,0 m2.K/W.
Dakconstructie
De dakconstructie bestaat uit houten spanten. Later worden er grillig gevormde betonnen schaaldelen op het dak geplaatst, waardoor de uiteindelijke blobvorm ontstaat. Uiteraard worden de schaaldelen ook allemaal ter plaatse geprint.
Waarom de keuze voor houten spanten? Kan het dak niet volledig meegeprint worden? Hendriks: “Wij willen ervoor zorgen dat het bouwproces zo efficiënt mogelijk verloopt. Je moet niet geforceerd alles willen printen. Soms is het logischer om er bijvoorbeeld kanaalplaatvloeren op te leggen. Hier kiezen we voor houten spanten met schaaldelen. Als je namelijk het dak wil printen, moet je eerst bekisting plaatsen met steigers. Dan ben je toch weer bezig met extra handelingen, mensen en materiaal.”